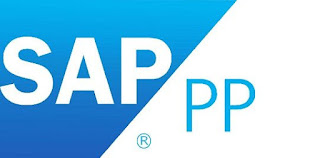
A production version
determines which alternative BOM is used together with which task list/master
recipe to produce a material or create a master production schedule. An
alternative BOM is defined if multiple formulations exist to manufacture same
semi-finished or finished material. Similarly, if a same material could be
produced using more than one resource, multiple routings (task lists) would
exist. Both the instances would require the creation of multiple production
versions.
For one material, we can
have several production versions for various validity periods and lot-size
ranges. At MYCOMPANY, we would have several production versions because of
multiple BOM alternatives as well as multiple RESOURCES that could be used for
the production of same materials.
Production versions are
used in Sales and Operations Planning (SOP), material requirements planning
(MRP), process order creation, and product costing to select the most suitable
task list or recipe and the corresponding material list.
After we have created a production version, the material components of the relevant alternative BOM are available in the recipe as a material list or can be created from within the recipe. Only now we can enter material data specific to a recipe, such as the component assignment to operations and phases.
A production version comprises the following data:
- Details on the material that the company wants to produce, for example, the material number and storage location where the material is to be stored
- General data about the production version includes:
- Key, lot-size range, and validity period of the production version
- Information on whether the production version is locked
- The date of the latest consistency check (i.e. all the data required for the maintenance of a production version is complete).
- The assignment of task lists/master recipes to the production version.
If there are say two alternative BOMs for a given material and three
master recipes, six production versions for such a material would have to be
created.
At MYCOMPANY, currently production versions are not used. In SAP, Manager
QA would be responsible for maintaining the production versions at MYCOMPANY MyCompany.
Process
|
Description
|
Process owner
|
Triggering event
|
Create Production
Version
|
A production
version maps the relationship between a BOM and a recipe. Therefore, the QA Manager
would be creating a production whenever a new BOM or Recipe would be created
in the SAP system.
While defining the
production version, the QA Manager would also set the lot size (batch size).
Multiple
production versions may exist for a similar type of product.
|
QA Manager
|
When SAP landscape is being created or when a new material would
be brought into production.
|
Edit the validity
of the production version
|
Each production
version once created in the SAP system has a valid to and valid from date.
The QA Manager may edit any of these dates on a need basis.
The QA Manager can
also edit the lot size of the production version
|
QA Manager
|
As and when
required.
|
Lock Production
Version
|
If the QA Manager
wants that particular production version should not be used for production
for a certain period of time, he may decide to lock it.
|
QA Manager
|
As and when required.
|
No comments
Post a Comment